Understanding the Different Types of Industrial Coatings
Industrial coatings appear everywhere. They protect a diverse array of products from corrosion, wear and tear and decay, as well as bringing an aesthetic and colorful appearance to the coated surface or product. With OEM applications ranging from:
- Building products
- Outdoor structures and equipment
- Sports and play equipment
- Cars, boats and planes and related accessories
- All other types of transportation equipment
- Appliances and machinery
- Construction and agricultural equipment
- Safety and security equipment
Well-chosen industrial coatings make manufactured products last longer and look better. The variety of possible coated surfaces is huge: All types of metals, wood, plastics and composites, rubber, glass, leather, and more. Almost any material used to manufacture an OEM product is a candidate for a protective industrial coating.
Manufacturers usually apply industrial coatings during the later stages of production. The finishing process, using the formulated coating material, protects and strengthens their valuable OEM product.
The range of characteristics of an industrial coating is quite wide. Your formulator will work with you to create the desired result and performance. In addition, it is important to develop a product that is useful to the technicians in the application process of your operation.
We’ve compiled a short list of some commonly used types of higher performance polymers in OEM industrial coatings. These polymers are available to be formulated in modern, low solvent or waterborne systems, as needed. Here, we describe some benefits each brings to their applications:
Polyurethane Coatings
Manufacturers use polyurethane coatings in a wide array of environments, often as a protective final coat over other custom formulated industrial primers. Polyurethanes resist abrasion, and can enhance durability to withstand wear and tear and abuse.
These coatings maintain color and can have an attractive, high-gloss finish, if desired. Aliphatic polyurethane coatings have good UV and environmental durability. Such coatings are a good choice for outdoor applications.
Aromatic polyurethane products resist degradation in wet conditions or underwater, but they tend toward fading when exposed to UV light. These coatings can work well in interior environments.
Two component polyurethanes do require protection for workers when applied, as with many other types of chemical processes. They are available in low VOC formulations.
Epoxy Coatings
These coatings normally consist of an amine curing agent blended with an epoxy polymer. Think of the double-tubes of epoxy glue you might use to secure a strong adhesive bond of one material to another. Formulators can alter the mix ratios (and ingredients) of epoxies to create a wide variety of characteristics. This gives users a unique coating to meet the demands of numerous environments.
Epoxy coatings bond well to many different surfaces. Epoxies resist weathering and abrasion extremely effectively. Epoxy coatings also withstand higher temperatures than most other coating materials. If properly formulated, epoxy materials can resist heat levels to many hundreds of degrees Fahrenheit!
Epoxies are often applied in two or three part systems. As a base layer, a user might specify a zinc primer for maximum corrosion protection. The epoxy would be applied over this primer. In a three part system, consisting of a zinc base, an epoxy binder and a final topcoat, a manufacturer may specify a polyurethane topcoat, for superior aesthetics and performance.
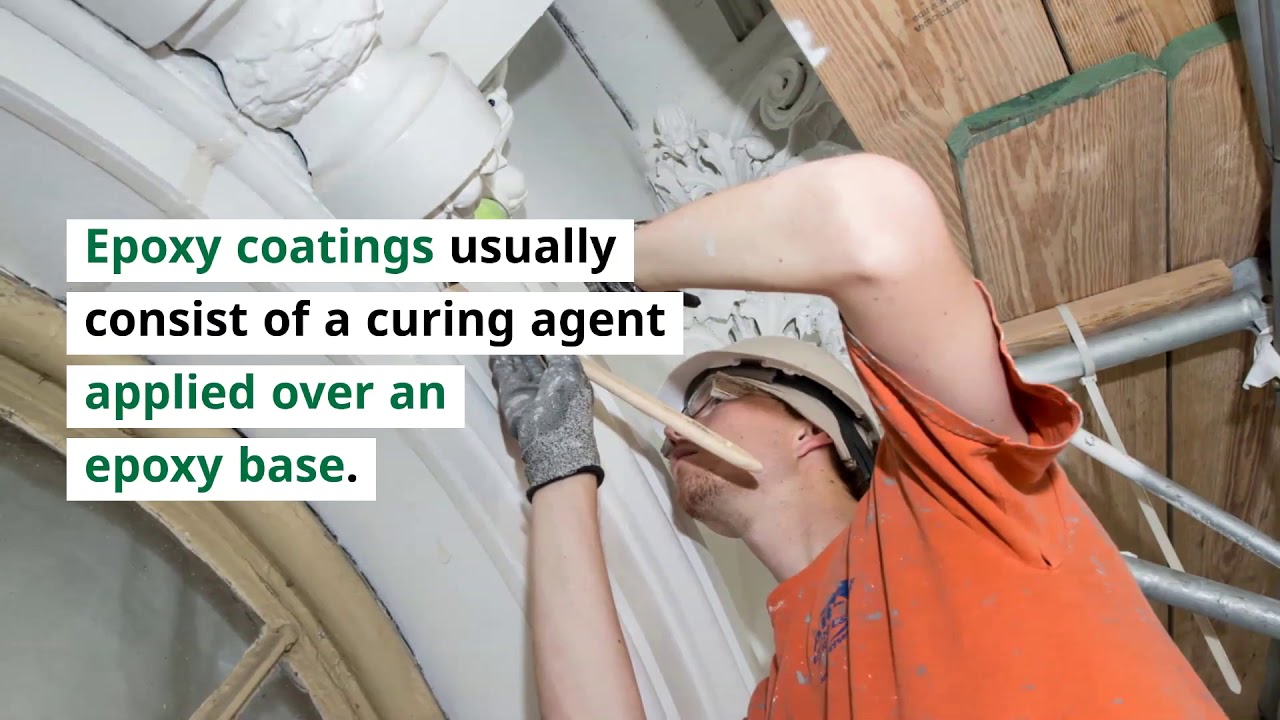
Alkyd Coatings
Alkyd coatings are proven, workhorse industrial and OEM coating materials. When applied to prepared substrates, alkyd coatings resist the effects of many different environments. They may be custom formulated to function effectively in interior, exterior, underwater, and underground settings.
Formulators adjust the components used to create custom alkyd coatings to adapt to a variety of conditions. Alkyd coatings may take longer to dry than other coatings, since they must be permeable to oxygen. As such, heat is often applied to speed the chemical curing reaction.
Zinc-Rich Coatings
These high performance coatings use zinc dust as a rust and corrosion preventative pigment. Organic zinc coatings are often made with epoxy or polyurethane resin binders, since high performance pigments justify high performance polymers.
Zinc coatings are particularly effective when used on steel, and provide dual function corrosion protection; both a galvanic and a polymeric barrier. Zinc-rich coatings are durable and resist abrasion.
Acrylic Coatings
Acrylic coatings have many advantages, including quick-drying and high gloss capability. They make great adhesion-promoting primers. Acrylics often require fewer ingredients and can increase the coated product’s corrosion resistance.
Find the Coating You Need
With so many different types of industrial coatings, Aexcel chemists can create one that precisely meets your OEM requirements. At Aexcel, we produce custom industrial coating formulations tailored to your specific substrate, end use and application needs.
Contact Us today for more information.