What Are The Advantages of Dip Coating?
Some complex parts that need coating do not lend themselves to spray, powder, or other widely used application methods. Dip coating is the process of choice for finishing materials full of nooks, crannies, and other hard-to-reach areas, provided these hard to reach areas can be drained. Manufacturers have turned to a dip process for nearly a century to paint difficult metals, ceramics, plastics, PVC, and other geometrically challenging component parts and products.
Industrial Dip Coating Process
The dip coating application process can be distilled into four stages.
- Pretreatment: Dip coating requires a controlled environment and a clean surface ready to receive the coating. This often requires a solvent or phosphate bath to cleanse the substrate and sometimes a sand blasting treatment to abrade the surface and to promote adhesion and efficient material transfer.
- Immersion: First, the material is immersed (dipped) into the coating at a constant speed. Prior to immersion, it may be necessary to pretreat the part with a primer to ensure the surface is clean and ready to accept the coating.
- Dwelling: The mandrel remains fully immersed in the dip coating for a specified period of time.
- Withdrawal: The mandrel is withdrawn at a constant rate, free from any judders to allow for a uniform, smooth finish. The faster the withdrawal speed, the thicker the application, since the faster withdraw speed pulls more of the coating onto the substrate before the coating can flow back down into the solution. Higher viscosity coatings also apply thicker in a dip coating application than low viscosity coatings with all other factors being equal.
Why Use Dip Coating?
There are several unique advantages of dip coating. A quick look at some of the common applications illustrates these advantages:
- Dip Coating for Metal HVAC Components: Perhaps the most vital advantage of dip coating is its ability to provide complete coverage to substrates with challenging geometries. For example, metal blower wheels like the one pictured to the right, are used in centrifugal fans in the HVAC and air pollution control industries. Commonly referred to as a ‘squirrel cage,’ the blades on the wheel are critical to the fan’s essential function, but make it a nightmare to spray or powder coat. Imagine a technician trying to spray a coating into the hundreds of crevices on the wheel, much less at a uniform thickness or in an efficient manner. With a dip coat, however, the coating flows over the entire surface, providing uniform coverage with relative ease.
- Dip Coatings for Tool Handles: Manufacturers often have two choices when they want to put a soft, graspable finish on their handles: injection molding a sleeve for the handle or applying a dip coating. Dip coating offers the same effect as injection molding, but in a much simpler, more economical industrial process.
- Dip Coatings for Metal Warehousing Racks: Metal warehousing racks are often dip coated due to their open geometry. Spraying racks like the ones shown below would be extremely inefficient and it would not make sense to incur the capital expenditure associated with installing a powder coating line to coat these materials. Dip coating systems present similar advantages for chain link fence manufacturing.
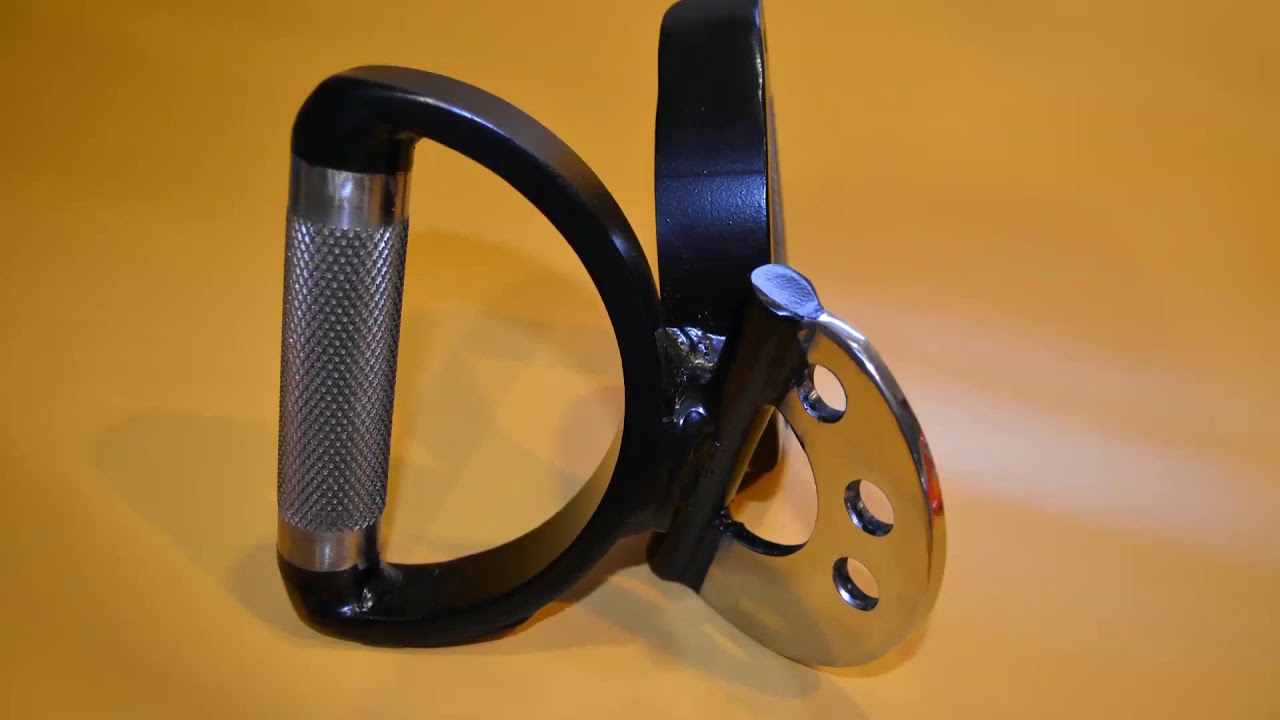
Other Advantages of Dip Coatings
Dip coating lines are also highly efficient, minimal waste systems, since any excess paint simply drips back into the dip tank to be used in the next round of application. Compare that with spray coating lines, where a significant portion of paint ends up on the walls and floor surrounding the coated material. Purchasing agents with spray lines must factor this in when deciding what quantity of paint to purchase, whereas they can be assured that most, if not all the paint in a dip coating line will wind up in its desired location—on the part to be coated. Dip coating also lends itself to automation given its relatively simple, repetitive process.
Dip coating is not a perfect system and should not be used for all coatings applications. If parts are too light relative to the coating, they may float upon immersion, making it difficult to achieve the desired finish. Film thickness can vary from top to bottom (commonly referred to as the wedge effect) with lower bottom edges more heavily coated. Dip coatings are also susceptible to sags and runs if they are not specifically formulated to guard against them as a result of gravity during cure time.
To avoid these issues, it is important to work with an expert formulator who understands your dip coating process and desired properties. Dip coatings can be formulated for a variety of cure types, including conventional thermal, UV, or even infrared techniques. They can also incorporate an abundance of surface effects to provide a unique finish.
Does your facility utilize a dip coating line? Having issues achieving proper coverage for your complex parts? Let’s talk about whether you are using the optimal coating system!
