A Guide to Metal Coatings
Coatings protect metal components and objects from damage like corrosion. Metal parts can be vulnerable to a variety of corrosion types, such as:
- Caustic agent corrosion from chemical exposure
- Galvanic corrosion from electrical contact
- General corrosion
- Localized corrosion
- Stress cracking
Fortunately, there are a wide variety of protective coatings to prevent metal parts from corrosion. These materials can be applied through different processes such as electroplating or electroless plating, spraying, and sputtering, facilitating complete coverage of vulnerable metal surfaces.
There are many protective coating materials and processes to choose from, and each is designed to address specific substrates and end-use environments.. It's important to also keep in mind environmental and regulatory issues when choosing a coating. Metal coatings can be formulated to meet cure time, VOC, gloss, and other desired properties.
Common Coating Processes for Metal Substrates
Different types of coatings bond to the metal substrate in varying ways. Five of the most common coating processes include:
- Electroplating: This ion plating process alters the ionic makeup of the surface so caustic agents, electrolytes, and moisture are less likely to cause corrosion. This method is ideal for complex surfaces that can't be fully coated through other means.
- Electroless Plating, or Conversion: This set of processes transforms the surface layer of a material into a corrosion-resistant surface. Black oxide processes, for example, oxidize the surface and transform it into a microporous, blackened surface.
- Hot Dipping: Just like the name implies, parts are submerged in a liquid coating. This process is often used for metal parts that face extreme conditions or that have complex geometries difficult to evenly coat with a spray gun.
- Brush or Roll Coat: Arguably the simplest method for applying paint, protective material is brushed or rolled on. Most common for simple surfaces where all areas can be easily reached, especially for field-applied coatings.
- Liquid and Powder Spraying: Liquid spraying may be used to apply paint or other liquid coatings to complex geometric areas that are difficult to reach with a brush or roller. Powder spraying uses an electrostatic charge to fully cover a substrate with a powder coating. The larger and denser the part, the more energy is required to charge it for powder coating.
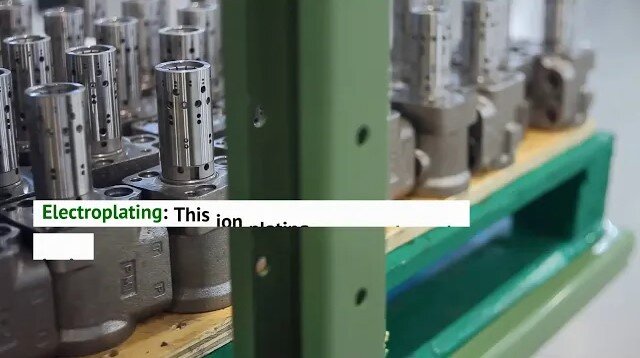
The Benefits of Coating Metal Parts
Coatings are popular because they provide significant, long-lasting benefits. Some of these benefits include:
- Durability and surface strength, especially for high-contact parts
- Electrical conductivity, which is useful for industrial and commercial components
- High-quality aesthetics, especially with polished surfaces
- Resistance to damage—metal coatings resist abrasion, chemical damage, corrosion, electricity and galvanization, and operational wear
- Improved torque and easy lubrication for fasteners and similar parts
Industries Served
Nearly every industry uses metal coating solutions to improve the physical characteristics of parts of and substrates. Aexcel serves the following industries:
- Aerospace
- Agriculture
- Architectural
- Automotive
- Consumer Goods
- Electronics
- Fasteners/Small Components
- Food-Handling
- Industrial
- Marine
- Petrochemical
- Storage Tanks
- Warehousing
Metal Coatings by Aexcel Corp.
Aexcel has 50 years of experience formulating metal coatings to simple and complex substrates. Our company has 500 custom-formulated products and the expertise necessary to pair any metal products with the right coating solution. We have experience in the following:
- Custom formulating coatings for difficult substrates and end-use environments
- Adhering to a wide variety of regulatory, environmental, and industry standards
- Toll paint manufacturing and private label partnerships under confidentiality agreements
Browse our industrial coating materials to learn more about our metal coating formulating services and products. Once you’re ready, please request a quote to get started on your next coating project.